The sales & ERP software we built for our client provided a seamless integration of various departments and processes.
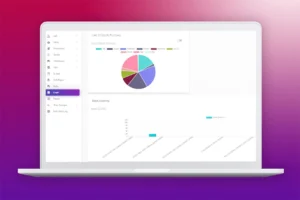
The Client
With over 35 years’ experience, our client’s high-quality inks are used across industrial and food manufacturing production. With a reputation second to none for service, quality and value, our manufacturer has a customer base covering all major continents, with export representing over 40% of total sales. Operating from a state-of-the-art facility near Bath, our customer has high manufacturing capabilities and efficiencies along with extensive laboratory facilities and offers the flexibility of bespoke product development to meet customers’ needs.
The Problem
The customer has been using a unique and bespoke ‘Unix’ application for the manufacturing process of their company which has evolved and has been added to over many years with the company’s continued expansion. The system was fully supported internally by one employee who has subsequently retired, leaving the company in a vulnerable position with a legacy and largely unsupported system.
Their previous solution had several drawbacks:
- No reporting function
- No access management
- Unsupported technology
- 3rd party applications cannot be integrated, limiting internal information sharing
The Solution
The software application we built for our client provided a seamless integration of various departments and processes in one robust scalable platform. The solution was flexible to handle their wide range of existing and incoming stock, raw materials and intermediate products, while also managing the safety testing and QC data associated with them.
- Ability to run complex reports
- Jobs trackable
- Fully auditable
- Customised dashboards
- Ability to import legacy data
- Backup solutions
- ASP.Net modern technology
